模壓成型 是一種廣泛使用的制造工藝,用于生產由復合材料、熱塑性塑料和熱固性塑料制成的高強度部件。完成一個成型周期所需的時間——即周期時間——會根據多個關鍵因素有所不同。本文將探討影響模壓成型時間的因素,以及完成模壓成型過程通常需要多長時間。
影響模壓成型時間的因素
有幾個因素會影響模壓成型周期的長短。以下是最重要的幾點考慮:
-
材料類型:像 SMC(片狀模塑料) 和 BMC(團狀模塑料) 這樣的熱固性材料通常需要更長的時間,因為它們需要固化。熱塑性塑料的成型時間通常較短,因為它們不需要固化。
-
模具設計:復雜的模具設計,具有復雜形狀的模具需要更長的時間來填充和固化。高效的模具設計可以縮短周期時間。
-
零件厚度:較厚的零件需要更長的時間讓熱量均勻滲透,因此周期時間較長。
-
溫度:較高的模具溫度可以減少固化或熔化時間,但過高的溫度可能會導致缺陷。
-
固化時間:固化可以確保熱固性材料正確硬化。所需的固化時間可能從幾分鐘到超過30分鐘不等,具體取決于材料和零件尺寸。
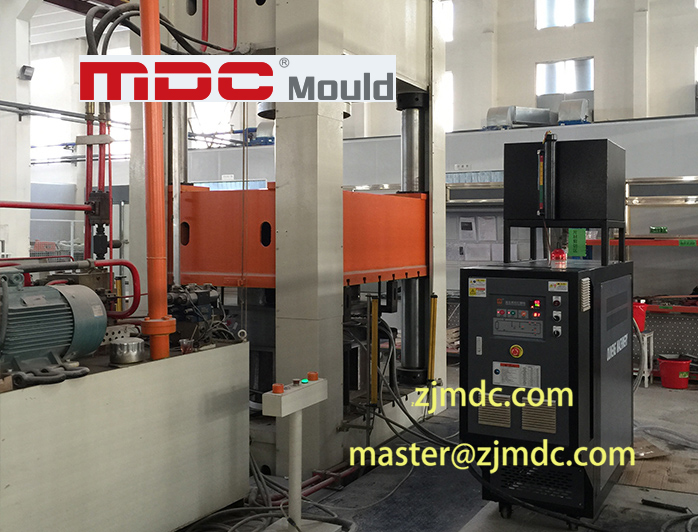
典型的模壓成型周期時間
模壓成型的周期時間通常在 1到10分鐘 之間,但對于復雜零件或較大的組件,可能需要更長的時間。具體時間取決于材料、模具設計和零件大小:
-
簡單零件:由熱塑性材料制成的薄而簡單的零件,周期時間可能為 30秒到2分鐘。
-
復雜零件:對于由 熱固性材料 (如 SMC 或 BMC) 制成的零件,周期時間通常在 5到10分鐘 之間。
-
較厚零件:需要更多材料和時間來固化的較大或較厚的零件,周期時間可能超過 10分鐘。
對于高產量的生產環(huán)境,如 汽車 或 航空航天部件制造,優(yōu)化周期時間對提高效率至關重要。制造商不斷致力于在不影響產品質量的前提下縮短周期時間。
模壓成型工藝分解
以下是模壓成型工藝的典型階段及其相應的時間:
-
預加熱(可選):預加熱材料可以減少周期時間,通常需要 1到3分鐘。
-
材料裝載:將材料放入模具中,通常需要 30秒到1分鐘。
-
模具閉合與加壓:模具閉合并施加熱量和壓力,持續(xù)時間為 30秒到10分鐘。
-
固化時間:此步驟對于熱固性材料至關重要,時間范圍為 2到15分鐘。
-
冷卻(可選):某些熱塑性零件可能需要冷卻階段,持續(xù) 1到3分鐘。
-
零件頂出:一旦零件固化或冷卻后,從模具中頂出,耗時為 10到30秒。
減少模壓成型時間的策略
有幾種方法可以在不犧牲質量的前提下減少模壓成型的周期時間:
-
優(yōu)化材料流動:改善材料流動可以確保模具腔體更快填充。
-
預加熱:在成型前預加熱材料可以減少壓制和固化時間。
-
自動化:自動化的裝載和頂出系統(tǒng)可以簡化工藝流程。
-
多腔模具:使用多腔模具可以同時生產多個零件。
-
優(yōu)化模具溫度:先進的溫度控制系統(tǒng)可以保持最佳模具溫度,從而減少周期時間。
結論
模壓成型 的時間可能會因材料類型、零件厚度、模具設計和溫度等因素而顯著變化。周期時間通常在 1到10分鐘 之間,但較大或更復雜的零件可能需要更多時間。通過優(yōu)化工藝中的關鍵環(huán)節(jié),如固化時間、材料流動和自動化,制造商可以顯著減少周期時間并提高生產效率。
了解模壓成型的時間長度對于管理生產計劃和滿足交付時間至關重要,尤其是在 汽車、航空航天 和 消費品 等行業(yè)中。